真空高压铸造铝合金车身后纵梁轻量化设计
文章来源:《汽车工程》
发布时间:2020-10-27
通过材料选择、结构设计、工艺分析和性能分析阐述了某电动车型真空高压铸造铝合金后纵梁的轻量化设计。
传统钢制后纵梁总成由后纵梁、后纵梁加强板和安装支架等钢制冲压件拼焊而成,如表1所示。结构复杂,零件约15个,整体质量约13.5 kg。改用一体压铸铝合金后纵梁可在保证原有性能大幅度提升的前提下,实现后纵梁的模块化和轻量化。
表1 钢制拼焊后纵梁总成
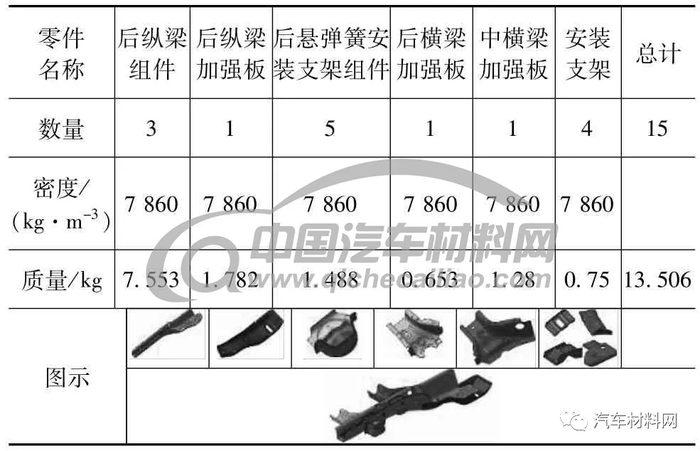
目前真空高压铸造铝合金所用原材料可分为3类:Al-Si系列、Al-Si-Cu系列和Al-Si-Mg系列,均可进行后续热处理。Si元素的加入可显著改善合金的流动性,抑制高温脆性,当Si含量在9%~12%时,铸造铝合金的铸造性能和强度都较好[9]。经过行业内一些车型的不断探索和验证,目前各种性能指标较为均衡,且技术比较成熟的材料是AlSi10MnMg。
材料足够的拉伸断后延伸率和折弯角可以确保零件材料有良好的塑性,是铝合金零件在铆接时铆接点不发生开裂的前提条件。一般而言,高压铸铝件的断后延伸率都低于3%。因此,为进一步提高塑性,还须对产品进行后续热处理,使其在长期服役的条件下形状和尺寸变化能够保持在规定范围内[10]。表2为真空高压铸造铝合金后纵梁经T7热处理后的性能指标。
2.1 后撞工况下的耐撞性设计
后纵梁是汽车发生倒车碰撞或追尾事故时的主要受损部件,其耐撞性能的好坏直接决定汽车安全性能的优劣。
汽车发生后撞时,白车身下车体后端分为A和B两个区域,如图1所示。A区域主要产生相对稳定的轴向碰撞变形,是主要的能量吸收区。B区域在后纵梁设计时应避让底部底盘系统,且纵梁前端连接电池包,为避免电池包碰撞时发生挤压变形,造成电池损坏,后纵梁需要一定的弯曲刚度来抵抗弯折变形,主要起传递碰撞载荷作用,其传递碰撞力约占总碰撞力的60%以上。
基于不同区域的不同功能要求,将后纵梁设计成由两个不同刚度的部件组合而成,分别称为后纵梁前段和后纵梁后段。前段主要抵抗变形,采用铝合金真空高压铸造而成;后段则通过变形吸收碰撞能量,采用铝合金挤出成型。本文中主要讨论真空高压铸造铝合金后纵梁前段的轻量化设计。
2.2 后纵梁结构拓扑优化
拓扑优化多应用在结构的概念设计阶段,是在给定的设计空间内找出最优的材料分布。同时可在不同工况要求下,帮助提取载荷路径[11]。
为更好地进行轻量化设计以及后续结构设计方案的制定,在概念设计早期阶段对后纵梁前段进行拓扑优化。首先基于汽车车身真实的试验工况,设置车身弯曲、扭转、前撞、侧撞、后撞工况下的边界条件;其次确定后纵梁前段的设计空间和非设计空间,非设计空间主要是后排座椅、后排座椅安全带、后副车架等安装点以及与门槛梁、后纵梁后段的搭接面等;最后以设计空间单元的密度为变量,最小应变能为目标,总体积分数<0.3为约束条件进行优化。
分别提取弯曲+扭转+前撞+侧撞+后撞、后撞、弯曲+扭转+前撞+侧撞工况下后纵梁前段的拓扑优化结构,如图2所示。从图2(a)可以看出,后副车架和座椅安装点等功能区材料分布较多,非功能区材料分布较少。纵梁空腔区域分布一条贯穿纵梁前后的随形加强筋,用以传递X向载荷,抵抗弯折变形。对比综合工况与单一工况拓扑结构发现:传递路径主要来源于后撞工况,如图2(b)所示。图2(c)为弯曲+扭转+前撞+侧撞工况下的拓扑结构,空腔区域材料分布密度较低,故交叉分布加强筋以抵抗变形,提高纵梁刚度。
拓扑优化使车身结构在满足最大刚度的同时实现后纵梁结构的轻量化,为后纵梁前段结构设计中各区域料厚的确定和加强筋的布置提供参考。
2.3 后纵梁结构设计
一体铸造后纵梁结构,其自身强度刚度较高,但不同截面形式对车身性能影响较大。表3示出两种典型后纵梁截面:H字型和几字型。在材料面积近似相同情况下,计算两种截面的抗弯和抗扭性能。其中,抵抗弯曲变形的能力用惯性矩表示,抵抗扭转变形的能力用扭转常数表示。可以看出,几字型截面的抗弯和抗扭能力更强。
截面形式确定后,考虑后纵梁前段X向分别连接门槛梁和后纵梁后段,底部须避让悬架包络,因而承载式车身的后纵梁常呈拱形。Y向与后地板连接,根据后地板布置可在连接区域增加翻边搭接后地板面板,结构如图3所示。壁厚根据功能需求有所不同,与钣金连接区域及上下功能面壁厚定义为3 mm,非功能面壁厚为2.5 mm,如纵梁侧面。为利于轻量,结合拓扑优化材料密度分布结果,局部区域可分段确定壁厚,如虚线框中壁厚为2.5 mm。
对于压铸件,随着壁厚的增加,铸件内部气孔、缩孔、缩松等缺陷会增加,设计加强筋时应尽量避免通过加厚来提升强度刚度等,因此在进行铸件结构增强时优先考虑增设加强筋[12]。后纵梁铸件加强筋设计主要依据以下原则:首先,根据拓扑优化结果,在纵梁空腔区域布置随形加强筋,以传递载荷,随后沿此加强筋交叉布置Z向或与Z向呈一定角度的加强筋,以提高纵梁刚度;其次,为增加翻边强度,在翻边的根部做加强筋局部加强,以减小热处理后变形;最后,考虑轻量化,加强筋整体做成内凹弧形,以最大限度减少不必要的材料使用,如图4所示。
由于铝合金和钢在导热率、导电率和熔点等方面的差异,以及熔化焊时导致的零件变形和界面脆性相[13-14],具有较高工艺兼容性和良好经济性的传统电阻点焊技术难以实现铝合金与钢的可靠连接,因此铸铝件与其他零件连接采用冷连接,如自冲铆接(self-piercing rivet,SPR)、流钻螺钉(flow drill screw,FDS)和螺栓连接。
SPR是通过铆钉穿透铆钉端板材之后,在铆模的作用下铆钉尾部的中空结构扩张刺入铆模端板材,产生咬边效果来实现连接。后纵梁翻边与其他冲压件采用SPR连接,如表4中后纵梁与封板之间采用两层SPR连接,与后地板、座椅横梁采用3层SPR连接。
但当连接点的某一侧为封闭腔体时,SPR需配合凹模实现的双边连接工艺无法应用。FDS利用流钻螺钉的高速旋转使连接材料摩擦生热而塑性变形,同时将螺钉旋入材料实现螺纹连接,如与后纵梁后段挤压型材之间采用FDS连接,如表4所示。
对于铆枪不可达的位置,采用螺栓连接,如表4中与门槛梁之间的连接。对扭矩和疲劳性能要求高的安装点(如副车架、座椅等),采取嵌入钢制螺纹套的设计,如表4中与后副车架之间的连接。
由于铝合金压铸后纵梁较长且空腔区域布置了一条贯穿的随形加强筋,选取铸件轮廓最大面为分型面,以便于铸件脱模。最后,为减小压铸过程开始阶段的卷气,在铸件长度方向上选取较为平直一侧设置内浇口,如图5所示。铸件末端设置阀A与阀B,负责抽取型腔内的气体,在铝液到达阀芯之前施加压力进行关闭,以保证型腔内达到高真空状态。此外,铸件填充末端设置溢流槽,以储存混有气体和铝液的残渣,控制金属液的流动状态,防止局部产生涡流。
浇注开始时,铝液初始温度为 700℃,以0.25 m/s的慢压射速度进入浇道和内浇口,当铝液充满所有内浇口后,压射速度提升到3 m/s,使铝液快速充填型腔。图6为铸件的温度场模拟结果。可以看出,铝液填充平稳,浇注顺序合理,型腔中的空气随着铝液的推进被顺序挤出,100%填充后,铸件整体温度均高于AlSi10MnMg材料的液相线温度,因而铸件因铝液温度下降出现冷隔的风险较小。
图7 为铸件的速度场和气压模拟结果。由图可知,内浇口处铝液流速约40 m/s,状态良好。铸件整体气压值在0.3 MPa以下,阀A与阀B的位置设置比较合理。
4.1 后撞工况仿真分析
车辆后撞工况中,后纵梁前段须有一定的刚度来抵抗弯折变形,以降低电池包发生挤压变形的风险,后纵梁后段发生压溃变形,吸收一部分碰撞能量。50 km/h后撞工况下,防撞梁、吸能盒、后地板及后纵梁后段发生压溃变形,吸收大部分碰撞能量,后纵梁前段几乎不发生变形,电池包壳体入侵9 mm,塑性应变0.14%,电池包周边及内部部件无尖锐物挤压,电池包安装点区域X向和Y向入侵量分别为0.15和0.09 mm,电池包合成加速度峰值为15.1g,电池包冷却系统、控制系统和内部线缆塑性应变为0,满足设计目标,结果如图8所示。
4.2 安装点刚度分析
真空高压铸造铝合金后纵梁集成多个安装点于一体,包括后副车架、后排座椅等安装点,需要满足一定的刚度要求来抵抗零件由于共振引起的失效。CAE分析结果如图9所示。由图可见,后副车架和后排座椅安装点静刚度值满足设计目标值。
动刚度是衡量结构抵抗预定动态激扰能力的特性。若干扰力频率远小于结构固有频率,动刚度与静刚度基本相同;若干扰力频率远大于结构固有频率,结构变形较小,即动刚度较大;若干扰力频率与结构固有频率相近时,出现共振现象,此时动刚度最小,即最易发生变形。动刚度不足会对整车的乘坐舒适性和疲劳寿命产生不利影响。动刚度计算公式[15]为
式中:a为响应点随频率变化的加速度,m/s2;X(ω)为响应点随频率变化的位移,m;F(ω)为激励点随频率变化的载荷,N;ω为圆频率,rad/s;f为固有频率,Hz;K为响应点随频率变化的刚度,N/m;IPIf为IPI响应分析所得曲线上对应的纵坐标值,m/s2·N。
当频率 f=fi=i(i>0)时,由式(4)得出频率 fi时的动刚度为
为便于对结果处理,一般直接采用IPI响应曲线进行分析,并采用分析点的等效动刚度K a与动刚度目标值K d比较以对连接点的动刚度特性进行分析。等效动刚度K a公式推导如下:
将式(7)代入式(6)得到该连接点的等效动刚度K a为
式中:SIPI-K a为 IPI分析中 IPI_K a响应曲线所包围的面积;Δf为计算频率步长。
图10为后副车架左前和左后接附点在X、Y、Z 3个方向的IPI分析结果。曲线IPI_K a为IPI响应分析曲线,两条曲线IPI_K d为目标动刚度的IPI响应曲线。由图可知,曲线IPI_K a所包围的面积小于目标曲线IPI_K d所包围的面积,表示后副车架左前和左后接附点在X、Y、Z 3个方向的等效动刚度大于目标值,满足设计目标。
通过材料选择、结构设计、工艺分析和性能分析阐述了某电动车型真空高压铸造铝合金后纵梁的轻量化设计。相比传统钢制结构,一体铸造技术实现了后纵梁结构的模块化和轻量化,得到的后纵梁质量约9.3 kg,比原件减轻31%。浇注系统设计合理,铝液填充平稳,后撞工况后纵梁前段几乎不发生变形,电池包未发生挤压变形,后副车架、后排座椅安装点静刚度满足目标值,后副车架接附点等效动刚度大于目标值,满足设计要求。
/
{data.addUser}
{data.content}
跟帖
查看更多跟帖 已显示全部跟帖